Press.
WATERJET CUTTING – now available at Superior
Superior Die Set has installed a ‘waterjet cutting’ machine to expand our cutting capabilities. We have always offered this service to our customers but chose to work with third party sources to handle our cutting needs. This was especially true when cutting slug holes in our Fortal aluminum die sets. Now with this machine under our roof, we can easily expand our range of use to many more options such as stripper plate openings in our new 4140 AR plate, or much smaller inside corner radiuses down to .020” on internal shapes. So exactly how does water cut through steel? A pump generates a flow of pressurized water for the cutting process that can reach up to 60,000 psi. Inside the nozzle the pressurized water passes through a small-diameter orifice and forms a jet of water. The jet then passes through a venturi section where a metered amount of granular abrasive, typically garnet, is drawn into the water stream. The mixture of water and abrasive particles passes through a special ceramic mixing tube and the resulting abrasive/water slurry exits the nozzle as a coherent cutting stream of abrasive particles travelling at very high speed. Through this process, clean definition, intricate geometry, and high tolerances are achieved and unrivaled by other cutting systems such as plasma and oxy-torch. Although more expensive, waterjet cutting has a unique feature, no use of heat, which broadens the horizon of use in such materials as glass, paper, aluminum, stainless steel, ceramic, and even wood. The limits on waterjet cutting capabilities are directly proportionate to the quality and tolerance required for the job. When customers request waterjet cutting, it’s almost assumed that other means of cutting is not satisfactory to hold the tolerances. For that very reason, Superior has set limits to its range of use so a high level of quality can be maintained. For example, the maximum thickness in steel plate for waterjet cutting is 3.5”, with aluminum a bit more. So to what tolerance can we waterjet cut to? This depends on so many factors such as the length of cut, thickness of cut, material type, and quality of definition. Although we can cut a piece 6’ x 12’, something this size would affect the overall tolerance is comparison to something very small. We have achieved tolerances down to +/-.005”, and can easily hold +/-.030”, but many dynamics need to be considered so each circumstance will dictate the offered tolerance.
STOP MILLING AROUND – Let Superior square your blocks…
Superior Die Set has expanded own plate machining services with the addition of a precision dual spindle edge milling machine. This new machine accurately mills the edges of plates to within .002” TIR with a maximum capacity of 16” high x 48” square. The dual spindle action rapidly removes material on two opposing edges, then indexes 90 degrees and completes the process so that all 4 sides are milled square and parallel. This high-speed action provides lower costs and reduced lead times The micro finish produced by this machine is better than most ground finishes, typically surpassing 32 Ra. Superior now has two of these Quick-Mill machines, with our original machine handling plates up to 9” high x 31” x 31”. We can even square plates much larger than 48” on our typical horizontal centers. This service is being applied to plate used in mold bases, die sets, fixtures, parallels, or anything requiring beautiful and accurate machined edges. A ‘Quick Mill’ video has been uploaded to our YouTube channel showing the capabilities of the machine along with some great examples
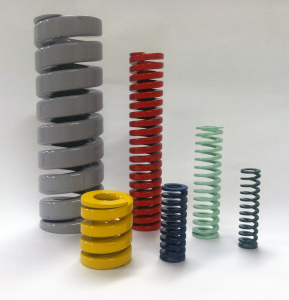
D-Line Springs
D-line springs offer an ISO-10243 solution for either new design or direct replacement of equivalent ISO parts (i.e. Danly Springs) but with the quality, reliability, and performance of Raymond. The duty ranges available in the D-line are the widest available, a total of 6, including ultra light duty (light green) and ultra heavy duty (grey) for extreme applications. Additionally the D-line offers sizes within specific duty ranges not previously available from Raymond. All Raymond die springs, including D-line parts, are manufactured from the highest quality materials. The industry leading manufacturing controls and quality have been a part of how Raymond products have been made for well over a century. The material cross sections designed & manufactured specifically for D-line springs are optimal for the ISO specification, delivering consistent rates and increased travel. Raymond D-line springs, while driven by an ISO specification, will work in inch applications, and have been designed & sized for exactly this. Whether your application for die springs is a die set or an OEM application D-line springs complete the Raymond portfolio of Die springs, the source of all your die springs.
Did you Say “Mild Steel”?
Since the first all-steel die set was introduced to the world by Superior Die Set in the middle of the last century, it has overwhelmingly become the material of choice in many facets of the metalworking industry related to tool holding. It is currently the most economical material choice for industrial applications that require a moderate amount of tensile strength, some resistance to impact – or “toughness”, good weldability, and good machinability. If you ask any machinist working with a steel die set, steel parallels, or steel fixture plates: “What type of material is that?” – chances are they may not know the particular specification of the steel that they are working with, and simply reply, “mild steel”. Mild steel is a very broad definition of steel with low carbon content. Other commonly used generic names are “hot rolled steel (HRS)” or “boiler plate (BP)”. These are general terms just like “mild steel” that really don’t get into the specifics of mechanical properties or steel chemistry. In reality, there are many different designations, grades or specifications of “mild steel” commonly used within our industry. Probably the most common is the ASTM designation for A36 steel. This material standard has very specific, but fairly wide specifications for carbon content as well as alloying elements. It is widely available and is considered a go-to standard material in construction of buildings, since the certification of its mechanical properties makes its engineered use predictable, and therefore safe. Another common specification is the AISI designation of 1018 or 1020 steel. This material standard is extremely specific as far as chemistry. The drawback, however, is that there is no guarantee on the mechanical properties of the steel. At Superior Die Set, we take great pride in the material we order because we know from decades of real-world experience that the mechanical properties of A36 are important, yet the consistency in chemistry is desirable, mainly due to the chemistry’s direct relation to the machinability of the steel. Specifically – we know that just specifying A36 is not always good enough. At the low end of the carbon range in the ASTM standard for A36 steel, the carbon content of the steel is so low that the material often becomes gummy during machining. This can result in, at best, inconsistent or slower than expected speeds and feeds – or, at worst, damaged cutting tools or pockets/holes out of tolerance as a result of damaged tooling. Every piece of #1 steel (A36 Mod) that comes from Superior Die Set is ordered with the specification “A36 with minimum carbon content of 0.15”. Every piece of #1 steel (A36 Mod) that comes from Superior Die Set is also tested and certified to meet expected mechanical properties AND Superior’s specification for steel chemistry. We can pull certifications for every piece of steel currently in our shop, as well as steel purchased within the last 10 years. We’ve been specifying and purchasing certified “modified” A36 for years and years. While machine operators at our customers may have noticed the difference, other personnel not working directly with Superior’s steel may not have realized the true value of #1 steel (A36 Mod) purchased from Superior Die Set. The bottom line is that the #1 steel (A36 Mod) we use in every die set and plate saves our customers money in the long run. Our customers are, and always have been, truly receiving a “Superior” steel.
Mold Components For Dies
Many dies are designed with guided stripper plates. Keyword: “guided”. Precision alignment of strippers is imperative for proper die functionality. Typically, designers will install extra pins and bushings for this purpose in a variety of fashions. The stripper plate area of a die is usually quite congested so fitting normal sized components there is quite difficult. Instead, designers use small diameter and low profile components that fit uniquely into tight clearance areas and thin plates. Although occasionally a ball bearing system can be used, mostly friction pins and bronze-lined or self lubricated bushings are installed. In the Superior Master Catalog, we have many component options for this use. Specifically, our die set type pins on pages 5060 and 5070 are displayed in a variety of sizes. Although there are many bushings to choose from throughout the book, we have a ‘low profile’ option – both with our Bronze-Rite™ lining. Page 5020 is a Superior standard bushing with a shoulder height of 1/2” (T) both in normal and long fit lengths (S) which offer extra bearing length (313P1005L). Similarly, bushings manufactured to Lamina™ standards are found on page 5030, again with low profile options. Another alignment system involves mold base components. These parts are headed to prevent accidental removal during production. Leader pins are offered in two styles (pages 4010 – 4020 and 4070) depending on press-fit length requirements. Ejector and core pins are well suited for this application also (see page 4150). Bushings (pages 4030 – 4060) can be purchased in many sizes and materials and don’t require toe clamps for an ultra low configuration. All Superior components can be downloaded in 3D models from our CADlink System available through our web site. Remember, UPS ground service is free when ordering on-line.