Press.
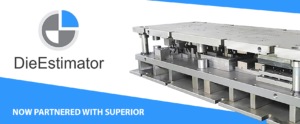
Superior Die Set Partners with Tool Planners, Inc.
Superior Die Set Partners with Tool Planners, Inc. Exclusive alignment to allow company to distribute DieEstimator die cost estimating software. Oak Creek, Wisconsin – November 3, 2020 – Steel and aluminum product provider, Superior Die Set Corporation today announced that the company has aligned with Tool Planners, Inc. The partnership positions Superior Die Set as the exclusive distributor of Tool Planners, Inc.’s DieEstimator software for global representation, effective immediately. DieEstimator, the die cost estimating software is a solution to the traditional, time-consuming quoting process that quickly adapts to the way you quote, providing Superior Die Set customers with greater precision and more accurate pricing compared to a ballpark estimate in calculating the cost of dies. “The DieEstimator software is a highly reputable brand to bring under Superior Die Set and offers us pronounced aptitudes in all the markets we serve,” said Mark Ullstrup, vice president of Superior Die Set Corporation. “The software will augment our core offerings and further define our position in the marketplace.” Jeff Bennett, Tool Planners, Inc. founder, owner and president, created the software to be a comprehensive product based on years of solving difficult die problems for metal stampers and die shops. After the software is installed, online training videos are available for quick use of the tool. Technology has enhanced the web-based software to afford complete mobility, as it is compatible with any Apple or PC device and effective on multiple browsers. “What makes DieEstimator unique from other software products is the strategic focus on the die-building experience, by die estimators for die estimators,” Bennett said. “Our company is a resource to solve issues in die estimation with in-person training, consulting and even the support of the PMA (Precision Metals Association).” According to Bennett, Tool Planners, Inc. selected Superior Die Set to represent the software based on its tremendous customer reach and effective marketing. Under the terms of the agreement, customers pay an annual fee with no complicated restrictions at an economical price point. About Superior Die Set Corporation Superior Die Set Corporation is a fourth generation, family-owned manufacturer of steel and aluminum products for the metal stamping, plastic injection molding, and forging industries along with fabrications used in machine tools, construction, and press automation since 1923. Located in Oak Creek, WI, Superior provides full in-house production capabilities, creating a cost-effective and streamlined process. Worldwide, Superior Die Set employs nearly 500 people for the manufacturing, sourcing, and support of the metalworking industries through two subsidiaries: Greendale Precision Services (http://www.gpspunches.com/) and ProPlastica (https://www.proplastica.pl/en/) Learn more at www.superiordieset.com. About Tool Planners, Inc. Tool Planners Inc. is an independent software and consulting company specializing in metal stamping die and production part cost estimating software, training and engineering services. Tool Planners, Inc. is known for its dedication to providing innovative software, training and services that help the industry plan, purchase and produce metal stamping dies and parts successfully. Tool Planners Inc. strives to create the industry standard for die planning and estimating, helping to reduce the total cost of manufacturing by eliminating unnecessary quoting. To learn more about how we help you better understand and control your manufacturing processes, visit us at www.toolplanners.com.
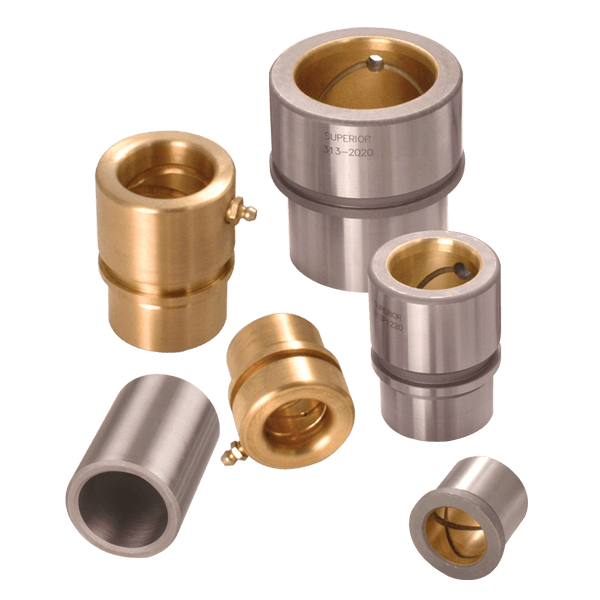
THESE ARE MY BUSHINGS OF CHOICE
Plastics Technology magazine, October 2020 edition, published an article ( CLICK HERE ) on guided ejector systems. On page 34 of the article, it states that “If you look around, you can find a supplier that offers hardened steel guided ejection bushings (48-50 Rc) with a bronze-plated inside diameter and with internal grease groove. THESE ARE MY BUSHINGS OF CHOICE”. Superior offers a premier bushing of the author’s choice….Bronze-Rite guided ejector bushing. The hardness on the steel portion of our Bronze Rite guided ejector bushings is 48-50 Rc. Also, these bushings are not plated; instead we use a special ‘fusion’ process to adhere the bronze to the steel. With this process, the bronze won’t peel, flake or chip off the steel. In fact, when we turn the bushings after hardening, the chip is half steel – half bronze and you cannot separate the two materials at the knit line. We add about .015/.020” per side bronze to the ID of the bushings, but that varies by diameter. This allows the bushing to be honed to whatever specification is required by the application. This is unlike plating, which only allows only several thousandths per side and would be instantly honed off. These bushings, with the hardened steel exterior and bronze ID, will not deform, oval, or elongate like solid bronze bushings typically do. Click here for more information: https://user-35215390377.cld.bz/Mold-Base-Components1/10/ Shop Online Now: www.supercomp.com
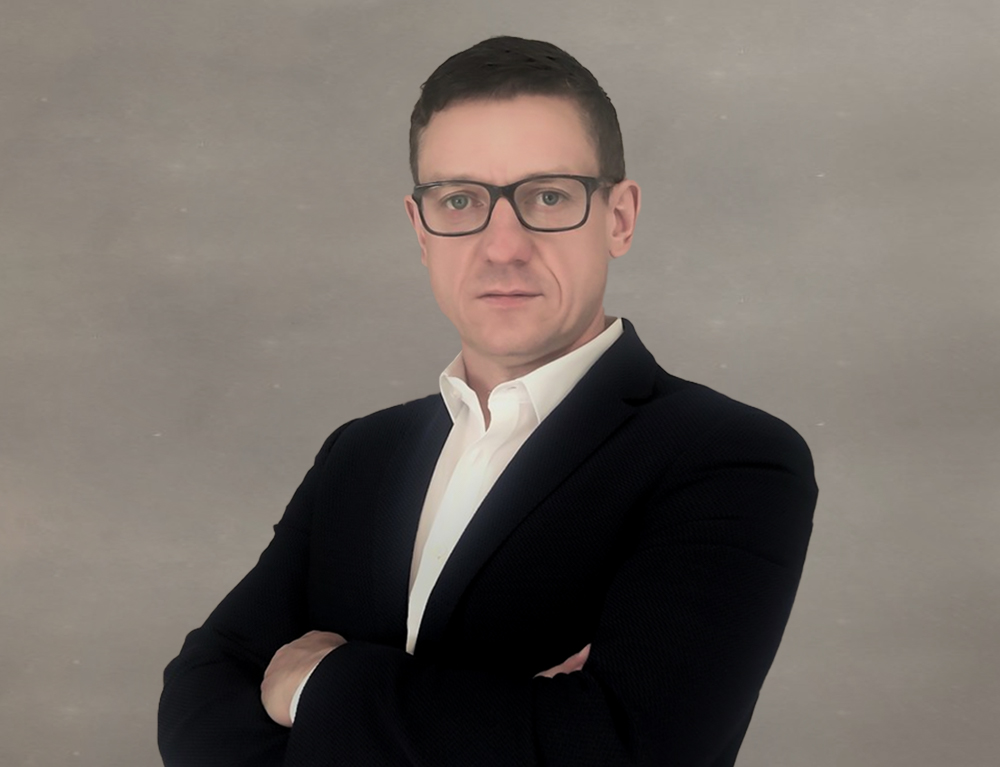
Welcoming Polish Leadership Team Member: Artur Piotrowski
Please join me in welcoming the newest member of our Polish Leadership Team, Artur Piotrowski who has taken on the role of General Manager, Poland effective August 4th. Reporting directly to myself, Artur will have oversight for the complete Polish operations. Artur holds a Master’s Degree in Management and Finance from the Management school at Poznan, an LSS Blackbelt certification and has a solid track record of success with organizations such as Saga Poland and the Unimould Group. His proven experience driving change through Lean methodolgies will help ensure that Proplastica continues to be the Supplier of choice in our market segment. Artur is a visionary leader whose organizations have realized tangible wins in terms of operations, sales, and fiscal growth during this tenure. We are very fortunate to have him on board and I personally look forward to working with him in the coming years. I’d also like to take this opportunity to thank the Polish Leadership team, namely Sławomir Szwankowski, Maciej Matuszewski, Marek Błaż and Robert Groborz for their tireless efforts over the past few months, especially in light of the COVID crisis. I can honestly say that Artur is inheriting a strong, successful team and I am excited for the potential they have working together. I know that I can count on all Superior Die Set employees to support Artur now as we work more closely than ever before as one global, Superior team! Best Regards, Martin Girga
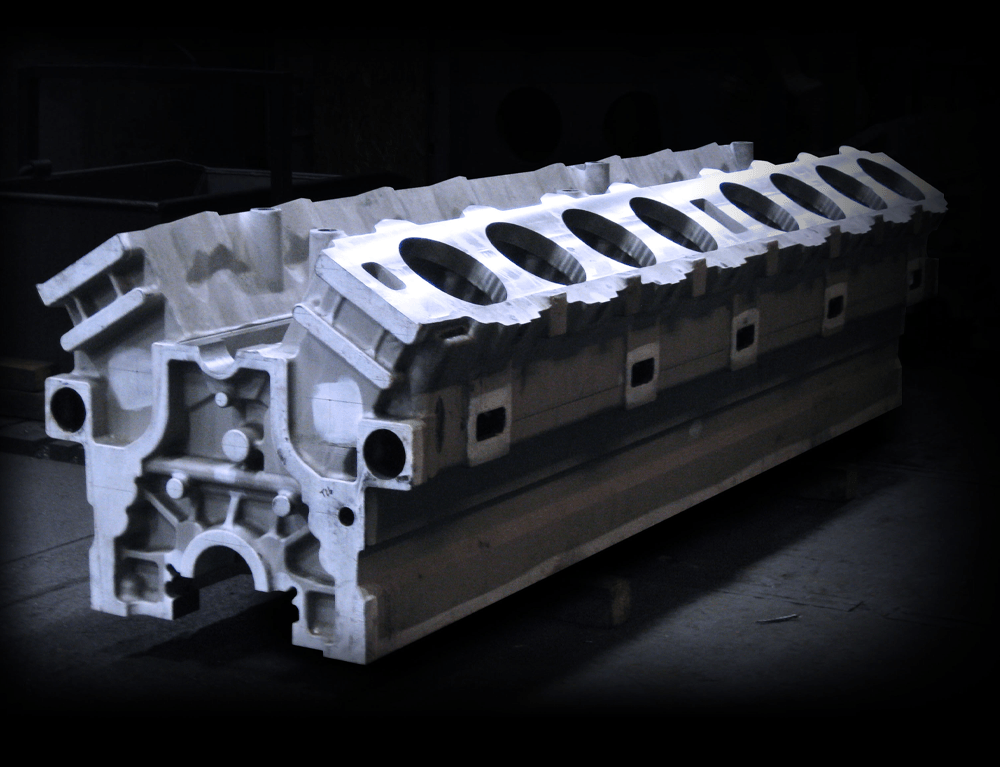
Vibratory Stress Relief
One of the lesser-known services that Superior Die Set is able to provide in-house is the process of vibratory stress relief (VSR). VSR is typically offered as a method to relieve residual stresses that are present as a result of flame cutting and/or welding. It is most often used on large weldments that won’t fit in Superior Die Set’s on-site furnaces, and can be an acceptable alternative to thermal stress relief (TSR). This article will provide a simple explanation and a bit of history about the VSR process, as well as a discussion of a few of the major benefits of VSR as compared to TSR. A Bit of History The principles of VSR have been in practice for many years. The earliest method involved a process called “natural aging”, where a metal (or wooden!) workpiece would be placed outdoors for up to a year-and-a-half, allowing the material to expand and contract naturally via the somewhat consistent fluctuation in daytime and nighttime temperatures. Blacksmiths used a technique called “hammer relaxation”, striking a metal workpiece repeatedly to induce high-amplitude vibration. Early metal-castings were even sometimes dropped from a considerable height into a pile of sand, again attempting to induce vibration with the end goal of relieving stresses. These processes, while somewhat effective, were uncontrollable, unpredictable, slow, and in some cases, extremely dangerous. The modern history of VSR developed in the midst of World War II. As the technology of aerial photography developed, it became easier and easier for the Allies to identify and bomb critical German facilities – in particular, those that offered heat-treatment. By 1943 the severe shortage of large castings forced German heavy industry to turn to fabricated weldments – but without heat treating facilities, they faced the problem of how large weldments could be stress relieved in preparation for precision machining. The Germans soon discovered that large fabrications transported by truck or rail from the weld shop to the machine shop, as compared with those that were welded and machined in the same or adjacent facilities, displayed superior dimensional stability during machining. This positive effect was described as a phenomenon, and wasn’t entirely understood – although engineers correctly supposed it was a result of workpiece vibration during transportation. After the war, and in particular as new types of steels and bimetallic materials were developed and utilized (some of which did not respond well to thermal heat treatment), demand increased for a way to reduce residual stresses without the use of a thermal process. And so began the experimentation with methods to generate vibration in a more predictable and cost-effective manner. Today’s VSR process is very straightforward. The workpiece (usually a large weldment) is placed on load cushions (shown as red). A vibratory motor and an accelerometer are fastened to the workpiece. Then a scan cycle is done on the workpiece by slowly and incrementally increasing the vibration frequency to determine the frequencies at which the workpiece resonates. Engineer’s Explanation: The peaks you see in the example chart above show the natural resonant frequencies of the workpiece, but the amplitudes are only a fraction of the workpiece’s potential amplitude. This is due to residual stresses present in the workpiece that are causing uneven spots of rigidity. Therefore the final step of the VSR process is to tune the vibratory motor to apply constant-frequency vibration at these resonant frequencies. This will cause residual stresses to decrease, the natural resonant frequencies to shift slightly, and the amplitude of the resonant vibration to increase. A Real-World Example and Alternative Explanation: To strike a large bell with a hammer will result in vibration and resonance. If there are any residual stresses left over in the bell because of the way it was manufactured, the bell will be too rigid at the spots of residual stress, and as a result will definitely not ring as loudly as it should and the sound will dissipate much more quickly (lowered amplitude and resonance). The VSR process will ring the bell at every frequency, in increments of 10 rings-per-minute, from 0 to 6000 rings-per-minute. The graph that is produced as a result of the test is a visual representation of the resonant frequency point(s) – i.e. those frequencies at which the bell should potentially ring the loudest. Then, the vibratory motor is used to force the bell to ring at exactly those frequencies, exciting the molecules of the bell’s material, and reducing the residual stress. A post-VSR ring of the bell results in a louder, more resonant tone because the residual stresses are reduced. The bell is less rigid overall and able to vibrate more than it did prior to the VSR. Main Benefits of VSR as compared to TSR The lead time for VSR is quicker (2-3 hours typical) vs. TSR (18+ hours), and VSR is less expensive, particularly if: The workpiece needs to be transported to and from a specialized heat-treatment facility The size of the workpiece demands special permits and flatbed truck transportation VSR can be used after rough machining to reduce machining stresses without the distortion caused by TSR A perfect example of this is a VSR application that is performed regularly at Superior Die Set: The part pictured is a 16 cylinder natural gas engine that is brought over from Germany, rough machined, and then vibratory stress relieved at Superior Die Set because the process has provided the customer the ability to hold tighter tolerances on the cylinder bores during finish machining. VSR does not cause distortion – TSR can cause distortion, especially for odd-shaped workpieces VSR is eco-friendly – using far less energy compared to TSR
Superior Die Set manufacturing mold bases for ventilator parts during COVID-19 pandemic
Superior Die Set has had to adjust operations during the COVID-19 pandemic, but CEO Martin Girga said the company has not been as negatively impacted as other manufacturers. The Oak Creek-based die casting company is recognized as an essential business during the COVID-19 pandemic because of the various industries it services, which include tooling, the automotive industry and stamping houses. As a result of that designation, and since many of the projects that Superior Die Set gets contracted to design, such as parts for upcoming car models that are expected to be released in upcoming months, business is not screeching to a halt. “We are feeling less of an impact than probably a typical company out there that doesn’t play in this market that we are in today in terms of tool and die shops. That’s favorable to us. That doesn’t mean that we may not get impacted later down the road,” Girga said. He said Superior Die Set expects more of a slowdown in the third and fourth quarters. According to Girga, many of Superior Die Set’s competitors supply foreign-made goods, which are currently experiencing supply chain issues. Because Superior Die Set makes what they sell, the company is able to control its own supply chain much more efficiently, Girga said. As the COVID-19 pandemic continues, the company has also seen an increase in orders for components that are being used to manufacture ventilators. The company’s first order from Accro Tool and Manufacturing in Burlington was received in the late afternoon on March 27. Accro Tool and Manufacturing is a plastic fabrication company that produces molds used on other products. It was an order for a custom mold base for a part used on a ventilator. The typical lead time on such a piece is five to seven work days. The Superior Die Set team delivered its first order in less than two days. According to an email from Accro, because Superior Die Set was able to produce the part so quickly, Accro anticipated tool delivery on April 6. “We’ve acted on this promptly realizing that this is a good thing for our company and to rally our troops around this to be able to help society and to be people that are sick,” Girga said. Superior Die Set has about 170 employees in Milwaukee, according to Girga. The company recently consolidated its Greendale facility with its Oak Creek headquarters. It also has operations in Poland. Girga said the pandemic is impacting all of its global sites, but noted that the Poland operations are still doing okay. Girga said that since February, the company has had an epidemic plan in place. So far, none of Superior Die Set’s employees have gotten sick. “We acted very quickly,” Girga said, noting that 90% of employees are working from home. “It’s a strange situation because you have people in the shop. You have people in the office. It’s different. It not only protects the people that are working from home. It also protects the people that need to continue to work here and continues to support the industry that we serve,” he said. Girga said the company is taking the appropriate steps to avoid layoffs. These steps includes Girga taking a cut in his own pay. He said the company also is taking steps at the top level to streamline and ensure the company is able to right size. “My idea right now at this point is the business while it’s slowed down, it’s still healthy enough for us that we want to make sure we’re retaining employees as much as we can,” he said. Girga added that if the company does struggle, it hopes to take advantage of some of the small business loans that are available to companies like Superior Die Set. Copyright- by Milwaukee Biz Original Article link here